
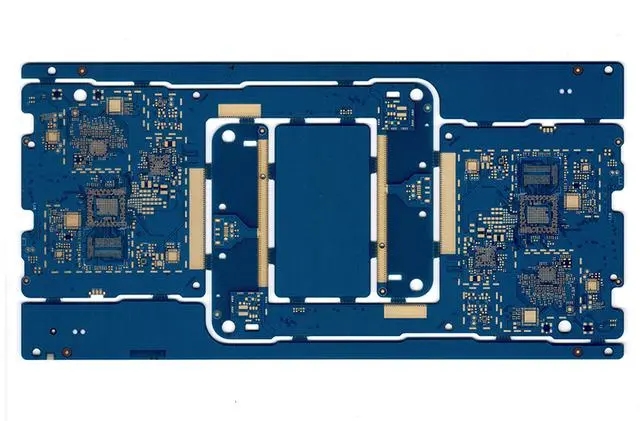
Soldering flux and cleaning for pcb circuit board -- what is cleaning?
The theMES of flux and cleaning are interrelated; You can't discuss the other without leaving one. The choICe of flux and cleaning process plays an important role in the production yield and product reliability of electronIC components. After welding, any corrosive substances left on the surface after welding must be completely removed.
This article will discuss various types of fluxes and the reasons for their use, and then discuss various types of cleaning materials and processes.
Flux is used to connect two metal surfaces. Joining through welding, brazing or soldering is basically the same, except that they are completed at different temperatures. All three joining processes use flux to remove oxides to form a strong bond between the joint surfaces. The main difference between these processes is that cleaning is not required after welding and brazing. But for electronic components, cleaning is the key process. After the connection process, the residues shall be cleaned and removed. Otherwise, field failure is almost inevitable, depending on the type of component and flux used.
Common metal surfaces connected by welding process are copper and tin. Like most metals, tin and copper have a natural tendency to oxidize. Therefore, in order to achieve metal to metal bonding between them, oxides need to be removed. Flux helps to provide a fresh and clean surface to complete the metal bonding between copper and tin (the same for both tin lead solder and lead-free solder), so as to achieve reliable solder joints.
Flux can also perform other functions at welding temperature. They can reduce the surface tension of the solder, expand the solder and promote wetting, so that the solder can form a firm and reliable solder joint. In addition, they can prevent further oxidation of solder during welding. In order to obtain additional oxidation protection, sometimes we also use nitrogen, but nitrogen does not play a role in the formation of metal to metal bonding, but it is essential for metal to metal bonding.
Consequences of using flux
We need flux, but there are disadvantages in using it. As we just discussed, we need flux to achieve good solder joints. However, once we finish welding, how do we deal with these flux residues? Shall we leave them on the PCB or remove them? The answer is: It depends. It is necessary to decide whether to leave them on the circuit board or remove them according to the hazard degree of these residues.
The type of flux residue or contaminant to be cleaned mainly depends on the type of flux used. Halides, oxides, and other contaminants can also be introduced during storage and handling. The use of aggressive flux will make welding easier, even if components and circuit boards are slightly oxidized and contaminated.
The selection of cleaning process depends on the type of flux, pollutant and component. For example, a mixed assembly using SMT components and through-hole components may require a cleaning process after reflow soldering and another cleaning process after wave soldering; However, a full SMT component on both sides may only need one cleaning process after the second side reflow..
When using the wash free flux, the circuit board may not need to be cleaned. In the wash free flux, chEMIcal substances such as carboxylic acid will activate and play their deoxidization function and then burn off, leaving no active chemical substances on the surface. But no wash flux needs perfect surface to complete welding. Otherwise, the welding defects will be too high.
There are four main types of flux, each of which is further subdivided into six different categories. In other words, we have 24 different types of flux to choose from. However, the last type of IN (inorganic flux) is not used in the electronics industry because it is too radical for electronic products. In fact, we only have 18 types of flux to choose from, instead of 24 in total, but it is still a difficult task. Table 1 briefly summarizes all 24 different types of fluxes.
The four main types of flux are: rosin (RO), resin (RE), organic (OR) and inorganic (IN). Each type of flux has 3 activity levels to choose from (low, medium and high). 50. Level M and H are divided into two categories: halide containing or non halide containing. Therefore, a total of 24 different flux categories are available. Fluxes without halides have a 0 at the end of their names, while fluxes containing halides have a 1 at the end of their names. For example, rosin flux without halide is calLED ROL0, while rosin flux with halide is called ROL1.
These naming rules also apply to RE, OR, and IN. The halides in L1, M1 and H1 are less than 0.5%, 0.5%~2% and more than 2% respectively. The activity of halogen-free flux comes from natural acid. The higher the flux activity, the better the welding effect. However, fluxes with higher activity must be properly cleaned to prevent corrosion on site. The non cleaning flux can be RO or RE with or without halide. However, OR flux must be free of halides (ORL0) and is classified as wash free.
Due to the high level of activity, the electronic industry usually does not use inorganic (IN) flux, which is often used by water electricians.
Cleaning materials and process types
It is generally considered that cleaning surface mount components is very difficult, because sometimes the height between surface mount components and circuit boards is very low, forming a very SMAll gap, which may intercept the flux, making it difficult to remove the flux during cleaning. In fact, if proper attention is paid to the selection of cleaning process and equipment, and the welding and cleaning processes are properly controlled, there should be no problem in cleaning surface mount components, even if corrosive flux is used. However, it should be emphasized that good process control is essential when using aggressive water-soluble flux.
The choice of cleaning process depends on the type of flux used. The cleaning process of different types of flux is briefly summarized.
Various solvents can be used to clean rosin and resin fluxes, such as organic solvents or water-based and semi aqueous solvents. Additives are required when cleaning with water solvent. If you want to clean the wash free flux (sometimes required), you can also use these solvents to clean, but sometimes you may need a special formula, and you can use water containing additives and non additives to clean the water-soluble flux.
The selected cleaning process can use solvent or deionized water or a combination of these two processes. In the past, CFCs (chlorofluorocarbons) such as Freon were commonly used as solvents, but their use was banned deCADes ago due to environmental problems. The industry has no choice but to use alternative solvents or water-soluble fluxes and pastes for cleaning, or to use low residue or no cleaning fluxes and pastes to achieve a "no cleaning" process.
The current technology of no cleaning or low residual flux eliminates the cleaning process. However, the use of cleaning free flux requires a clean working environment and a change in habits, which will not only affect users, but also their suppliers. In addition, the use of no clean flux may require a controlled welding environment to provide a process window compatible with its lower activity.
Since the use of fluxes that require cleaning and disposal of lead containing solvent wastes can cause environmental problems, the use of non cleaning fluxes is increasing. But we also need to keep in mind that the non cleaning flux is not as active as other types of flux. Therefore, unless the company and the parts and PCB suppliers take appropriate steps, the welding results may be lower than expected.
conclusion
No matter what flux, cleaning material or cleaning process is used, they all need to meet the same requirements. When higher activity flux is used, appropriate solvent shall be used for cleaning to remove any contamination that may cause site failure due to dendrite growth and corrosion. But how to know when PCB is clean enough? If you ask SIMilar questions, it means that the solder joints have caused reliability problems on site, and the questions are easy to answer, because J-STD-001 and IPC-A - 610 have formulated relevant acceptance or rejection standards. However, although specific requirements are specified in both standards, it is not easy to determine PCB cleanliness.
PCB manufacturing, PCB design and PCBA processing manufacturers will explain to you the soldering flux and cleaning of PCB - what is cleaning?.
然后
聯系
電話熱線
13410863085Q Q
微信
- 郵箱