
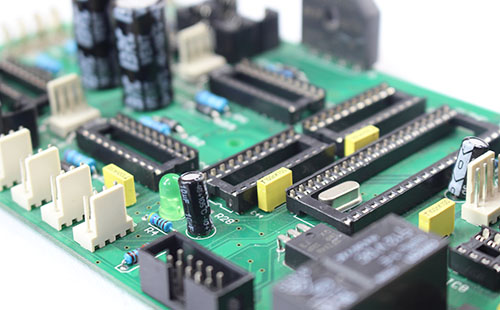
PCB Factory: What is the core concept of modern electronic assembly and connection?
PCB manufacturers, PCB designers and PCBA manufacturers will explain to you what the core concept of modern electronIC assembly is.
Modern electronic assembly should adhere to the core concept of "design is the source, material is the guarantee, process is the key, management is the root, and concept is the core", and abandon the old thinking mode of "technology is the basis of technology", which is SIMply limited to technology.
1. Design is the source
Ensure the correctness of the design, meet the requirements of DFM, DFA, DFR and DFT, and do not violate the provisions of prohibited and restricted design and process. Only by fully demonstrating and paying attention to the manufacturability, usability, detectability, manufacturing economy, quality stability, etc. of the design at the initial stage of design, can the dual purposes of "zero defect design" and "zero defect manufacturing" be achieved. Only such enterprises can provide high-quality electronic products with high cost performance ratio for the MARKet. The requirements for process quality control in the whole process of PCBA development and production cover typical assembly and welding process types, new components, new materials, new technology applications and key process quality control requirements. The combination of design and process, and the combination of process and process control, not only put forward the quality requirements and quality objectives of PCBA, but also put forward the design, material process optimization and quality monitoring measures to achieve the above quality objectives in great detail. This approach is the first time in all previous standards and specification systems at home and abroad to be praised as an international advanced level by doMEStic famous electronic assembly experts. The analysis of failure cases is very important, but it is also preliminary. The general reliability analysts basically analyze the failure phenomena from the perspective of case theory or technology; And we just need to make clear through case analysis what kind of design is wrong and has no manufacturability. At the same time, for the failure cases of highly reliable electronic products, which are mainly reflected in the phenomenon of violating prohibited and restricted processes and designs, we focus on what kind of design is absolutely prohibited. Through the above analysis, In particular, the first master and the chief engineer of product model clearly identified that the main cause of electronic product quality problems was the lack of manufacturability in design.
Taking the board level circuit as an example, DFM is a concurrent design that runs through the entire life cycle of PCB/PCBA. It is completely different from the lagging practice of most electronic enterprises' process work at present to participate from the back end of the product development and production industry chain, and also different from the current popular technology to participate in the manufacturability analysis from the end of the design; It is completely synchronized with the circuit design, that is, from the demonstration of the tactical and technical indicators of the product and the scheme design stage to the after-sales service stage of the product.
2. Material is the guarantee
Materials are the most fundamental and fundamental constituent elements in the process of electronic assembly welding. They include processing materials such as components and PCBs, as well as process materials/auxiliary materials such as solder paste, solder, flux, patch adhesive, cleaning agent, etc. Their quality is good or bad and whether they meet the requirements. Many quality problems of electronic assembly that directly affect the welding quality are often caused by defects in the physical and chEMIcal properties of the materials used. Material quality control is the basis to ensure the quality of electronic assembly. The basic objective of electronic assembly material control is: "All materials used in the manufacturing process, such as electronIC components printed circuit board, solder paste, solder, flux, patch adhesive, cleaning agent and other process materials/accessories, must meet the quality requirements of electronic assembly in all aspects of the production process, such as procurement, warehousing, storage, outsourcing, circulation." Made in China must go out of the strange circle of single imitation and "copycat", and cannot stay in the "important stage of understanding the concept of reliability and repeatability" forever. Any electronic product should pursue high quality and high grade; In order to achieve high quality and high grade, the rules of DFX must be followed first, and the process optimization design must be carried out, especially the due position and role of the process must be restored. Emphasize that design is the source, fundamentally solve the quality problem of circuit design, and fully demonstrate and pay attention to the manufacturability, usability, detectability, manufacturing economy, quality stability, etc. of design at the initial stage of design. Design for manufacturability and material quality control are the sources that affect the welding quality and reliability of electronic products. Based on the strategy of "prevention", we control and "prevent" the key elements that affect the welding quality from the source and process. The purpose is to reduce or even eliminate the congenital defects caused by design and material quality problems as far as possible.
3. Process is the key
Optimize the process parameters, and do not violate the regulations on prohibited and restricted processes to ensure that the assembly and welding quality meet the requirements of highly reliable electronic equipment. The inherent design lacks manufacturability defects and material quality problems, which are difficult to compensate by improving the process measures, that is to say, the process is not omnipotent! On the other hand, good design quality and material quality will not naturally lead to reliable welding quality, so process research and development must be carried out with optimization of welding process parameters as the core and establishment of a complete process quality control system as the goal. Foreign developed industrial countries have always put the research and test of process technology in a prominent position.
4. Management is fundamental
Efforts should be made to enhance the recognition of the leaders in charge of each enterprise on the necessity and importance of implementing DFX in the process of electronic product R&D and production. Efforts should be made to make leaders at all levels fully realize that the implementation of DFX is the only way for an enterprise to become bigger and stronger! Without a centralized and unified process research department and the support of powerful process personnel, the platform for implementing DFX will be lost.
5. Concept is the core
Circuit, structure and technology are the three major technical elements of electronic products, which are indispensable and complement each other; An advanced and perfect electronic product requires not only technologically advanced and economically reasonable circuit scheme and structural design, but also advanced process technology. The final realization of the product and whether it has market vitality depends to a large extent on the advanced level of process technology. For electronic products, the function of road design products, the form of structural design products, and the process of process design products. Poor design for manufacturability is the source of affecting the quality of electronic products. This phenomenon is mainly manifested in the THT period and the early period of SMT. In the THT period and the early SMT period, an electronic assembly engineer only needs to understand the structural principle and composition of the equipment. According to the expected reliability value and target of the design, he can assemble the equipment into independent products by relying on the accumulation of experience. In this period, the reliability of electronic products mostly depends on the correctness and manufacturability of the design.
The decision-makers of enterprises can purchase/introduce the finalized circuits from the market just as they purchase components when THT technology is applied to electronic products, then combine them according to the technical requirements of the products, carry out necessary tests according to the use conditions, and only design a few circuits. The "highlight" of product design is the electrical interconnection technology. This is a sign of technological progress and an inevitable trend of the development of advanced manufacturing technology.
PCB manufacturers, PCB designers and PCBA manufacturers will explain to you what the core concept of modern electronic assembly is.
然后
聯系
電話熱線
13410863085Q Q
微信
- 郵箱